The style of a SAG mill liner is driven by the material of building and construction and also the application, as well as limited by casting, molding, and taking care of constraints. For huge mills with wide inlet trunnions, in excess of 1.5 m, liner handling types of equipment are currently in common usage, and also this has actually permitted the development of large integral liner blocks, considering as much as 1.5 t a piece, Figure 1. This holds terrific advantage for minimising relining time, as there are fewer blocks to handle. As an example at the Kalgoorlie Consolidated Gold 2Mines (WA) 36ft SAG mill the variety of Outer Head Liners was reduced from 36 to 18 items and in doing so decreased the time to replace them by 9 hours at an expense downtime saving of regarding U$ 25,000 per hr. In this instance the liners areas are 3.5 t each. For smaller sized mills the liners need to be dealt with as well as mounted manually, so smaller blocks with removable lifter bars are normally favoured, Figure 2. A checklist of the main types of liners is offered, with talk about their application, advantages and also negative aspects:
1. Solid Liners – These have an integral lifter and liner, as shown in following. These have fewer pieces and are easier to install, but tend to have a high scrap weight as once the lifter section is worn down liner performance drops and necessitates change out.
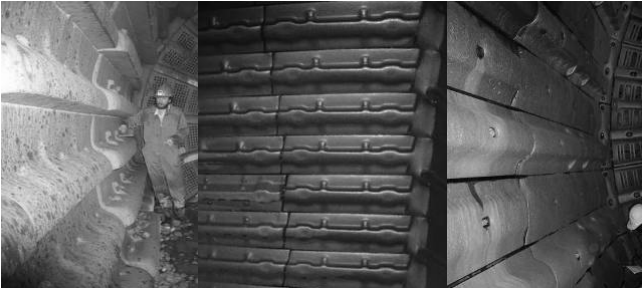
2.Removable lifter – The lifter can be changed rather than the complete liner, thereby maximizing liner life and assisting in manually relined mills. More pieces have to be installed and liners can move during relining and if not well secured against the backing liner the lifter can shift and work loose, this is especially a problem if the bolts begin to stretch.
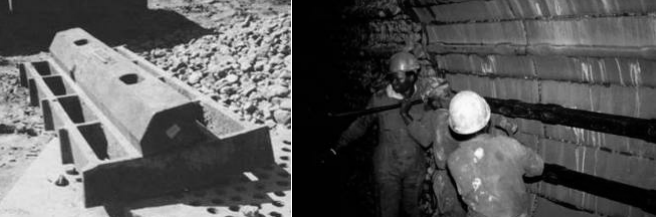
3. Grid Liners .A system that appears to be unique to Southern Africa, is pocketed grid liners, where the grinding media packs in the grid structure and forms an integral part of the liner, Figure 3. Often the liners have a flat profile, suited to the high speeds (85% to 90% of critical) that most of the older mills operate at. These liners have been demonstrated to be economically unbeatable for highly abrasive ores in small to medium size mills . They are light in weight and make use of the grinding media hardness to provide an effective wear material. They need to be manufactured in Manganese steel to wedge the steel balls, but the manganese steel spreads on impact and can make removal difficult. There is also the safety aspect to consider, of the risk of balls dislodging when the mill is entered for inspection or relining. The liners do require a thorough hosing down to prevent this.
4.Wedged liners – These were common in the first half of the last century, but are dangerous to install and no longer used. What is used now is liner blocks wedged in by bolted lifter bars, which allows simple castings of the liner blocks.
5. Integral wave blocks – These are commonly used in ball mills, and the profile of the liners has become sufficiently sophisticated to enable the liner profile to be maintained as the liner wears.
6. Uni-Direction Profiled Liners – The lifter has different leading and trailing profiles, Figure The profile can be better customised to suit mill speed and filling and therefore optimise performance, and it allows more material in the lifter for a given base width, but the mill must only run in one direction.
7. High–low double wave ball mill liners – These are a refinement of the wave liner, Figure 5. This was applied to Cadia Hill Gold Mine through evaluation of their existing wear profile and wear rate, and provided a more consistent wear profile through the liners working life. The correct wave face angle needs to be calculated and applied as an incorrect angle could lead to ball segregation and loss of grind.
An indication of our limited ability to accurately ‘design’ liner profiles is that few liners are optimal at original installation or in the post-commissioning set, and it is imperative as a user to vigorously pursue the improvement of the design, to get the most out of the liners. An indication of our limited ability to accurately ‘design’ liner profiles is that few liners are optimal at original installation or in the post-commissioning set, and it is imperative as a user to vigorously pursue the improvement of the design, to get the most out of the liners.