The finite element analysis software ANSYS was used in the numerical simulation of the frame of CJ411 jaw crusher and the main causes leading to the frame crack were analyzed. The accidental load led to the evolution of the defects in the casting member of the crusher that was under high stress, leading to the flaws. The high alternating stress p roduced in long term overload operation facilitated the rap id growth of these flaws, finally leading to the fatigue failure of the frame. On this basis, measures for repairing and improving the frame structure were proposed: to use welded carbon steel components to replace the casting members in the high-stress zone and to change the welding to bolting for the connection between the beam and side plates. The numerical simulation comparative analysis of the frame before and after the repair indicates that the repaired frame has a rational stress distribution, and the measures have not only fully utilized the material properties but also greatly reduced the fracture failure probability, achieving a remarkable improvement. This research has not only solved the practical problem but also provides a reference to the frame design optimization of jaw crusher.
Analysis The Reason Of Jaw Crusher Frame Cracked
CJ411 Jaw Crusher Geometry
The Sandvik jaw crusher is a compound pendulum crusher that is easy to adjust the size of the crushed size and has a deep and symmetrical crushing chamber. The frame consists of two rolled steel side plates, hollow cast iron castings at both ends of the frame and moving jaws. The overall geometric structure of CJ411 jaw crusher is shown in the following figure.
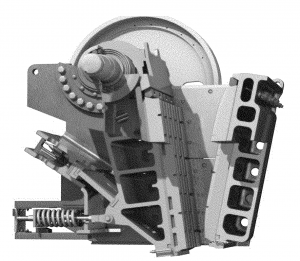
CJ411 Jaw Crusher Geometry
Numerical Simulation of CJ411 Jaw Crusher Frame
In order to analyze the damage reason for CJ411 jaw crusher in detail, the numerical simulation analysis of the frame was carried out by ANSYS software. Due to the lack of detailed geometric parameters of the original design, the main dimensions of the rack were obtained by mapping the prototype of the rack. Considering the symmetry of the rack, half of the model is built during modeling. At the same time, according to the characteristics of the force at the time of crushing, and the main object is the frame, the inertia wheel is omitted during the modeling, and the geometric details of the bearing, the front and rear walls of the crushing chamber, the moving jaw, the fixed jaw and the like are ignored. Finite element computational geometric model, please check the following figure.
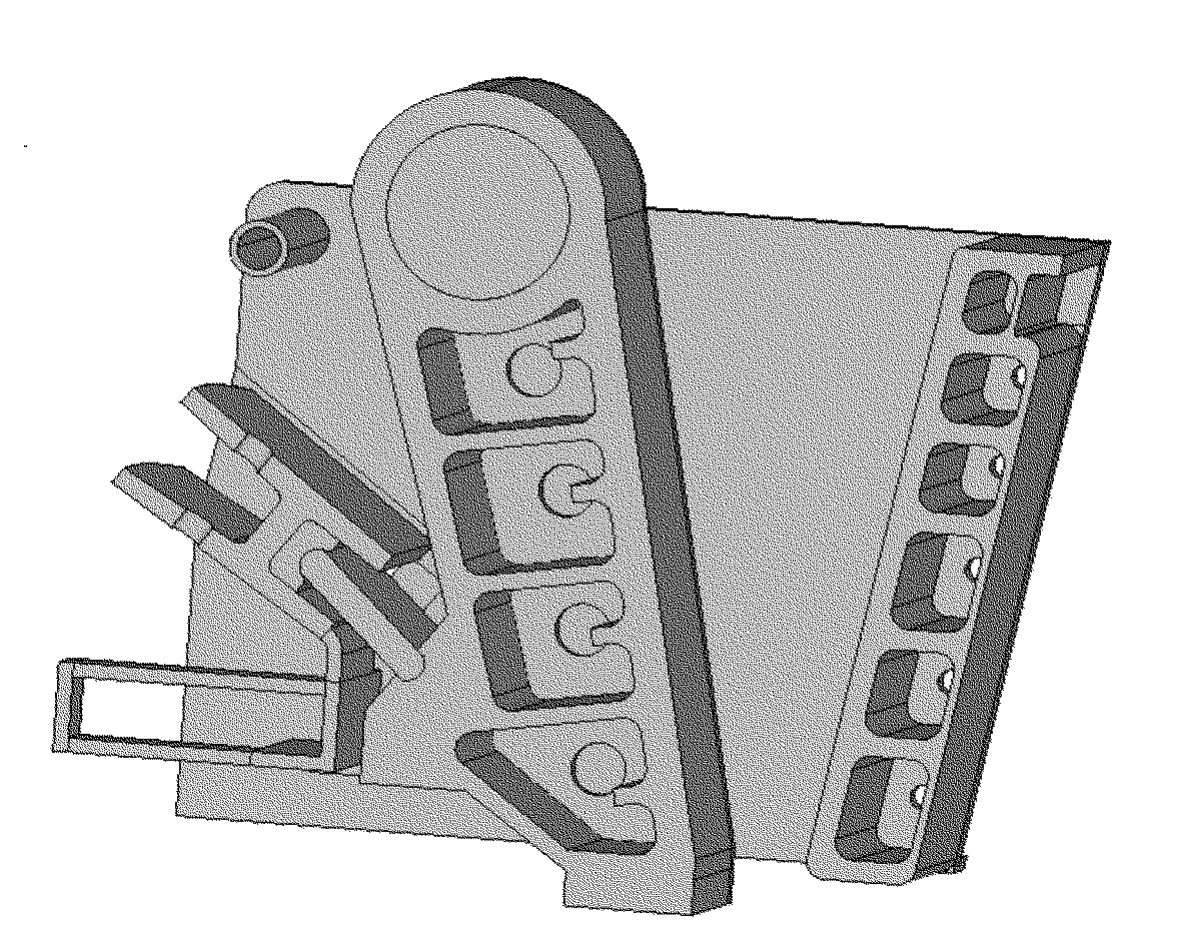
Finite element computational geometric model
The CJ411 jaw crusher is mainly used to crush molybdenum ore. Therefore, the compressive strength is 40 MPa, which is the main basis for applying the load by making a sample of the randomly selected molybdenum ore and performing a compression failure test. The SOL ID92 unit is used for free meshing, and the boundary conditions are set according to the actual working state. The finite element calculation model is established, static numerical simulation is performed, and the main results are calculated. Check the following picture:
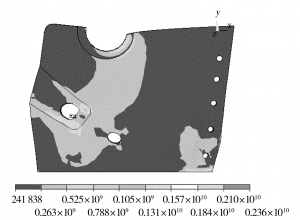
CJ411 Jaw Crusher Frame Stress Situation 1
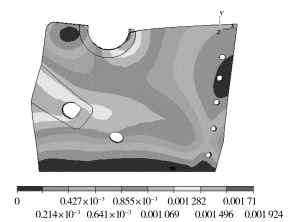
CJ411 Jaw Crusher Frame Stress Situation 2
Analysis of Damage Causes of CJ411 Jaw Crusher Frame
- During the working, the welded joint of the frame beam and the side plate limits the small-angle rotation of the beam, so that a relatively high-stress region appears in the frame beam and the side plate, and stress concentration occurs at the fixed support portion at the front end of the frame. This is an intrinsic factor that causes the rack to break.
- The frame beam and the front wall are cast members, and there are inevitable defects such as bubbles and impurities in the casting, which creates conditions for the generation of micro-cracks. Once the stress reaches a certain value, the defect will become a crack source, and then Crack formation.
- The investigation found that before the machine was destroyed, the machine was stuck with superhard substances (such as iron blocks), which caused the machine to die and caused the crack to expand rapidly. This means that the overload protection device – the connection plate is not protected so that only the frame can be severely damaged in the event of an accidental overload.
- The data show that the model is suitable for ore with a crushing strength lower than 35 MPa, and the measured breaking strength of the broken molybdenum ore in actual operation is 40 MPa, and the crushing granularity is close to the upper limit of the design of the model. In addition, in order to pursue production, the company operates uninterrupted and all-weather operation and does not adopt maintenance measures for periodic trouble-free active shutdown maintenance. Long-term overload operation is also one of the most important factors for rack damage.
Based on the above factors, the main reason for the failure of the frame is that the accidental load causes the cracker to be under the high-stress condition and the crack of the casting component is cracked. The high alternating stress environment of long-term overload operation facilitates the rapid growth of the crack and eventually leads to the rack.
CJ411 Jaw Crusher Frame Repair And Finite Element Analysis
Due to the high price of imported equipment, it is necessary to repair it. However, the measures of welding and thickening in the area where cracks occurred initially failed to achieve a good repair effect. After repairing, a new rapid expansion crack is generated near the weld seam after only one revolution without changing the working condition.
Therefore, new measures must be taken to improve the repair. According to the analysis, only avoiding the overlap of high-stress areas and areas with potential defects can eliminate the cracks that cause fatigue damage of the frame, thus prolonging the service life of the crusher. Repair improvement measures: will be high The cast parts in the stress area are replaced by carbon steel welded parts, which not only improve the strength but also reduce the potential defects; the connection between the beam and the frame is changed from casting to bolting, which reduces the mutual restraint between the frame and the beam during work and reduces the internal structure. Additional stress.
The specific steps are to cut the beam from the frame first, then use the steel plate to fill the part of the excavated frame with steel plate, and then bolt the welded beam to the frame. In order to overcome the stress concentration of the bolt hole, Thickened steel plates at the holes ensure that the frame will not be damaged by the stress concentration of the bolt holes.
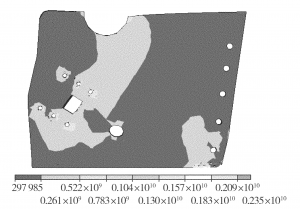
CJ411 Jaw Crusher Frame Stress Situation After Repair 1
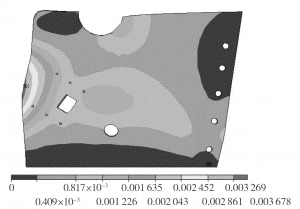
CJ411 Jaw Crusher Frame Stress Situation After Repair 2
Through the finite element numerical simulation analysis of the CJ411 jaw crusher produced by Sweden Sandvik Company, it is revealed that the main cause of the frame failure is that the accidental load causes the crusher to be under the high-stress condition, and the casting member defects evolve and crack, long-term overload operation. The high alternating stress environment facilitates the rapid growth of cracks and ultimately leads to fatigue failure of the frame. Based on this, the frame was repaired and improved. It was run for several months under the original working conditions, and no new cracks appeared. It can be seen that the repair improvement method is effective.
Combined with the results of this study, the following recommendations are made for the rational and effective use of the crusher:
- It should be accurately selected according to the actual working conditions;
- Ensure that the self-protection device is effective during normal operation;
- Strengthen equipment maintenance and avoid overload Running.