Cone Crusher Adjustment Ring Manufacturer
When it comes to cone crusher adjustment ring, MGS Casting had manufactured this cone crusher parts for many years. Our replacement parts can suit many brands cone crusher and span life can match the original parts.
Generally, the bowl is movably attached to the adjustment ring which is connected to the main frame. The size of the crushing gap can be adjusted by vertically moving the bowl with respect to the crushing head. As the bowl vertically moves with respect to the adjustment ring and main frame, the bowl and bowl liner move vertically with respect to the mantle. A conventional adjustment mechanism comprised of a hydraulic motor rotates the bowl with respect to the adjustment ring via the gear. The hydraulic motor rotates the bowl with respect to the main frame so that the bowl is vertically raised or lowered, thereby adjusting the gap size.
Cone Crusher Adjustment Ring Technical Requirements
Material Requirements
Chemical analysis (ladle analysis) ranges (% min./max.) shall be as follows:
C | Mn | Si | S | P | Ni | Cr | Mo | Cu | Fe |
0.25 | 0.7 | 0.2 | / | / | / | / | / | / | Bal |
0.35 | 1.75 | 1 | 0.04 | 0.04 | 0.5 | 0.25 | 0.2 | 0.3 | Bal |
Heat Treatment
All castings shall be delivered in normalized and tempered or quenched and tempered conditions, followed by stress relief and shall conform to mechanical properties specified in the table below. Minimum tempering temperature shall be 1100ºF (595ºC).
Mechanical Properties
Tensile Strength Min. PSI (Mpa) | Yield Point Min. PSI (Mpa | Elongation In 2” (50 mm) | Reduction of Area |
90,000 (620) | 60,000 (415) | 20% Min | 40% Min. |
Casting hardness shall be within the range of 179 – 223 HB. Locations of hardness tests and depth of hardening shall be per the casting drawing or purchase order instructions
Mechanical Testing
If a mechanical properties report is required , the procedure for pouring and treatment of the representative test coupons, preparation of the representative tension test specimens and the number of tests and retests conducted shall be in accordance with ASTM A 148 and A 781, selected either for normalized and tempered castings or for liquid quenched and tempered castings.
Mechanical Dressing
Runners, risers, fins and other cast-on pieces shall be removed and dressed down to blend with the normal profile of the casting surfaces. Sand, scale fins, etc. shall be removed from all keyholes, bolt holes, pinholes and fit areas. (Fit areas are defined as areas whose surface will have bearing contact with a component part.) For handling safety, all surfaces shall have no sharp fins or other sharp irregularities
All machined surfaces shall be coated with a rust inhibitor, and all surfaces to be painted shall be painted, per customer requirements, as specified by customer, except when noted otherwise on customer orders, as accepted by the customer. Where the casting drawing indicates subsequent machining, typically denoted by phantom lines or finish marks, the casting shall have adequate stock to enable 100% clean-up unless stated otherwise on the drawing and/or casting order.
Welding Repairs
We shall include all necessary welding parameters, type of weld metal, welding process, weld preparation, preheat temperature, minimum interpass temperature and post-weld heat treatment when deemed necessary by customer Engineering. Weld maps are required for all weld repaired areas. Weld repairs should, if possible, be made prior to final heat treatment of the casting. The hardness of welded areas and heat affected zones shall not exceed 223 HB.
- Minor Defects – A defect shall be considered “minor” when the cavity as prepared for welding is no greater than 20% of the actual wall thickness, but in no case greater than 1 inch (25 mm).
- Major Defects – A defect shall be considered “major” when the cavity depth as prepared for welding exceeds 20% of the actual wall thickness or is greater than one inch (25 mm) in depth regardless of the actual wall thickness.
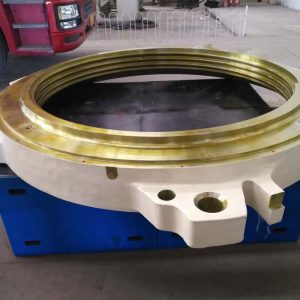
Cone Crusher Adjustment Ring For Australia
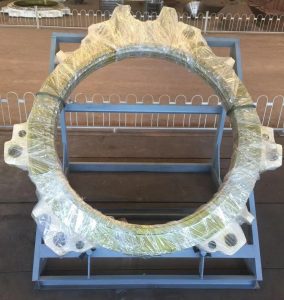
Cone Crusher Adjustment Rings In Package
If you have any questions or inquiries about cone crusher adjustment rings, contact our engineer freely.