High Manganese Steel Casting Porosity Problem
High manganese steel is widely used in casting jaw crusher parts, cone crusher parts, sag mill liner, and other casting parts. due to its excellent wear resistance and work hardenability. In the casting process, the formation of the pores of the casting is complicated and diverse, and it is difficult to define, and the scrapping or rework of the casting is extremely likely to occur. This paper focuses on the formation of high-manganese steel casting porosity, starting from the process and raw and auxiliary materials, and continuously practiced a set of effective methods to solve the casting defects of high-manganese steel.
Manganese Steel Casting Porosity
After the high-manganese steel castings are treated by water toughness or machining, they show different degrees of porosity defects, especially when the returning method is smelting, the whole furnace castings have porosity defects. Result in batch scrapping (about 80% of the entire scrap castings) and rework processing. After analysis, the oxidation castings are mainly intrusive and reactive pores; in addition to the above two types of pores, the returning castings are particularly serious. The location and form of existence are complex and diverse.
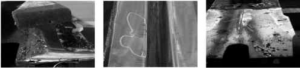
high manganese steel castings porosity problem
Manganese Steel Casting Porosity Causes
The gas has a certain solubility in the molten steel. During the cooling and solidification process, the molten steel is decomposed due to the decrease in gas solubility. The charge that is returned to the smelting process is the pouring riser of the casting, the cast steel, and the scrapped fork. During the melting of the charge, a large amount of nitrogen and hydrogen in the air are dissolved into the molten steel. At the same time, in order to ensure the recovery rate of the alloy, the smelting process is strictly prohibited from oxidizing the molten steel, and the gas in the molten steel cannot be removed by oxidation. When pouring, the temperature of the molten steel is lowered, the solubility of the gas is lowered, and the gas is precipitated. At the same time, the deoxidation of the molten steel is not good, and the internal carbon and oxygen react to precipitate a gas. The evolved gas diffuses to the hot or high-temperature portion of the casting, and if it is too late to discharge the mold, a precipitated pore is formed in the casting. It is usually distributed in the section of the casting or in areas with high temperatures such as risers and hot sections.
Manganese Steel Casting Porosity Solutions
- Reduce the amount of dissolved gas: Before the feeding, add 2.5% lime and 1.5% fluorite at the bottom of the furnace to make slag in advance, cover the surface of the molten steel, avoid direct contact of the molten steel with air, and reduce the amount of gas dissolved. Control the amount of lime and fluorite added. Adding too much, the slag layer is thick, which is not conducive to the outflow of molten steel gas; too little is added, the slag layer is thin, and the effect of protecting the molten steel is not obvious.
- Removal of dissolved gases: Oxidation smelting Through the oxidation period, carbon-oxygen reaction (C+O → CO ↑), a large amount of CO bubbles generated during the reaction floats, and the dissolved gases are carried together to form molten steel. Boiling, the gas discharges the molten steel, and the degassing effect is achieved. Therefore, the oxidized casting has few precipitated pores.
For the smelting of the return method without oxidation period, the principle of degassing by oxidation is used. At the time of smelting, limestone (CaCO3) is added at a high temperature of CaCO3→CaO+CO2↑. During the floating process, the generated CO2 gas carries the dissolved gas together and floats, causing the molten steel to boil and the gas to discharge the molten steel. Go to the purpose of degassing.Pay attention to the following points when adding limestone:
(1)Timing of addition: It must be added after the charge is completely melted to achieve degassing of the entire molten steel.
(2)Method of addition: Consider the low density of limestone and the protection of molten steel by the slag surface layer. Before the addition, about 70% of the steel slag must be discharged, and the method of gravity dumping into the molten pool is used to directly enter the molten steel by gravity, and a large amount of gas is decomposed in a short time, causing the molten steel to boil and achieve the purpose of degassing. .
(3) Addition amount and blockiness: The addition amount is about 3% of the molten steel, which causes the molten steel to boil for 10 to 15 minutes. Too little to add, the boiling time is too short, the degassing effect is not obvious; too much, easy to accumulate, and the non-conducting phenomenon occurs. The blockiness is 100 ~ 150mm, the block size is too small, easy to float on the slag surface; the block is too large, the decomposition is slow, and the boiling is not severe. Affect the degassing effect. - Prevent the internal reaction of molten steel: When tapping, add 0.2% rare earth and 0.1% silicon germanium aluminum crucible to the ladle for final deoxidation, reduce the oxygen content of the molten steel, and avoid the carbon and oxygen reaction inside the molten steel. At the same time, stable compounds formed by [S], [O], [H], and [N] in rare earth and steel fix the gas in the molten steel.
- The pores formed by the interaction between the molten steel and the mold (sand type, cold iron, etc.). After processing, the pores appear as clustered, diffusely distributed circular pores. The frog reaction pores mainly appear in the position where the cold iron is placed and the cold iron is placed. Cold iron position stomata: Individual cold iron surface is rusted or wet, reacting with molten steel during pouring: Fe+H2O → FeO+2H ↑, Fe2O3•nH2O+(n+1)Fe →(n+3)FeO+2nH ↑, C+FeO → Fe+CO ↑, gas is generated. Since the cold iron is not gas permeable, the gas diffuses and floats into the molten steel, and the cold iron chilled molten steel quickly cools and solidifies, and the gas does not reach the floating state to form pores. Cold iron clearance vent: When spraying paint, the coating penetrates into the molding sand too deep along the cold iron gap. After the coating burns, the water generated deep in the gap does not completely evaporate, reacts with the molten steel to generate hydrogen, invades the molten steel, and forms pores.
Solving the problem of porosity in high manganese steel castings
- Before the cold iron is used, shot blasting is performed to remove surface rust and oil stains.
- When the climate is humid or the weather is cold, the cold iron is easy to absorb moisture and preheated before use to evaporate water. It also contributes to the full combustion of the cold iron surface coating and the evaporation of moisture after combustion to prevent the reaction from forming gas. The heating temperature is 40 ~ 50 °C, the temperature is too low, the moisture on the surface of the cold iron is not fully evaporated, the temperature is too high, and the molding sand in contact with the cold iron will dry quickly before the earthquake, resulting in loose sand structure and low strength.
- After the paint is sprayed, the molding sand in the cold iron gap should be hooked out to avoid excessive penetration of the coating, resulting in insufficient combustion or moisture evaporation. After the paint is fully burned, the mold should be placed for 30 minutes. After the water is completely evaporated, the box can be buckled to ensure the drying of the mold.
- FT660 alkaline phenolic resin containing no harmful elements such as N, P, and S, and magnesia quick-drying coating with small gas generation. Reduce the reaction between molten steel and mold.
- Appropriately increase the proportion of coarse-grained sand in the peridot sand used for modeling to ensure the permeability of the molding sand.
- Since the lower surface of the mold is covered with cold iron, it has no gas permeability. When sculpting, increase the number of upper vents, increase the aperture appropriately, and open the attachment to the surface of the model; repair the venting groove on the side of the ear part of the mold parting surface (top surface of the casting); open the riser to communicate with the outside Add 4 exhaust plates to the upper end of the non-gate end casting to allow the gas in the mold to drain smoothly.
- According to the climate, the vacuum degree of vacuum hardening can be adjusted at any time to ensure that the gas in the sand gap is fully discharged and the molding sand is sufficiently dried.
In this paper, the stomatal defects that are prone to occur in the production process of high manganese steel frog casting are analyzed, and the causes of stomata formation are found out. The process and the improvement of raw and auxiliary materials are targeted, with emphasis on operational details. By tracking the quality of the castings, the scrap rate and rework rate due to porosity defects are greatly reduced. Very good results have been achieved.